In today’s global marketplace, maintaining high-quality standards is paramount for any manufacturing company. One effective way to demonstrate a commitment to quality is by obtaining ISO 9001:2015 certification. ISO 9001 is the world’s most recognized Quality Management System (QMS), and not only defines quality management principles but also serves as a benchmark for excellence. On this page, we’ll delve into what ISO 9001:2015 certification entails and why it’s a noteworthy achievement for Optmel.
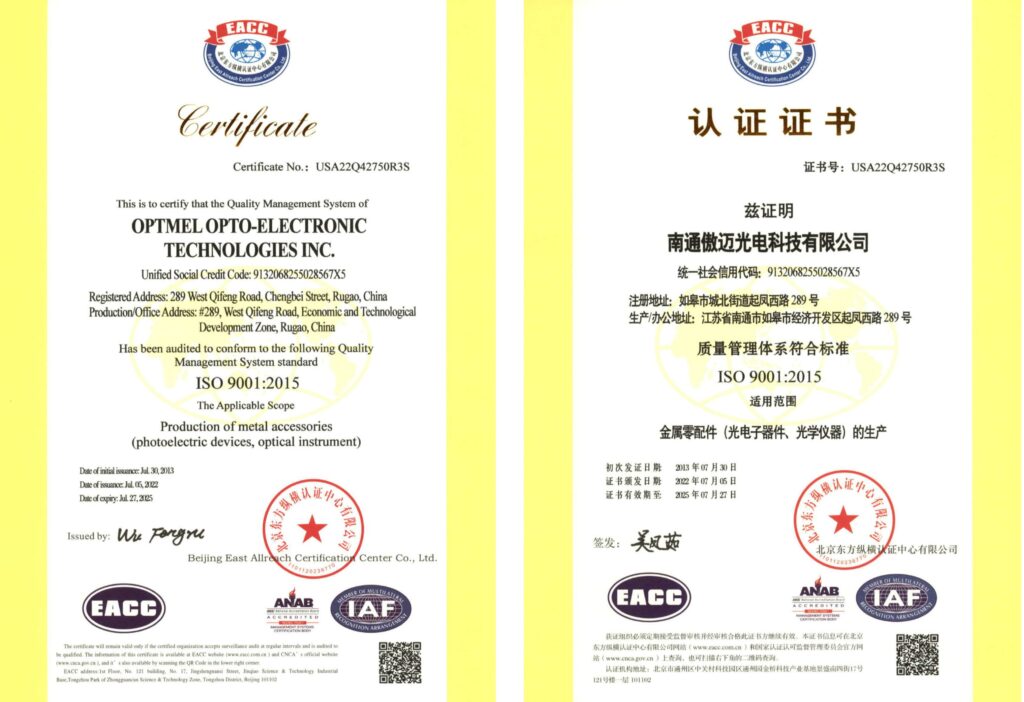
Understanding ISO 9001:2015 Certification
ISO 9001:2015 is a quality management system standard developed by the International Organization for Standardization (ISO). It sets out the criteria for a QMS and is based on a number of quality management principles, including customer focus, leadership, process approach, and continual improvement. The certification demonstrates a manufacturer’s ability to consistently provide products and services that meet customer and regulatory requirements while enhancing customer satisfaction.
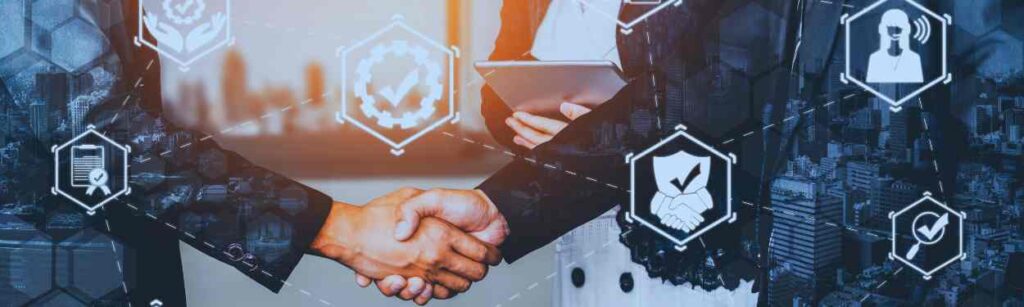
Key Elements of the ISO 9001:2015 Certification
1. Customer Focus: Understanding and meeting customer needs and expectations is at the core of ISO 9001:2015. Manufacturers must prioritize customer satisfaction and ensure their products or services consistently meet or exceed expectations.
2. Leadership: Strong leadership and commitment from top management are essential. This includes establishing a quality policy, setting quality objectives, and fostering a culture of continuous improvement.
3. Process Approach: ISO 9001:2015 emphasizes the importance of understanding and managing processes as a means to achieve desired outcomes. Manufacturers must identify and map their key processes, monitor performance, and make data-driven decisions for improvement.
4. Continual Improvement: Manufacturers must continually assess and enhance their quality management system, driving a culture of ongoing improvement in all aspects of their operations.
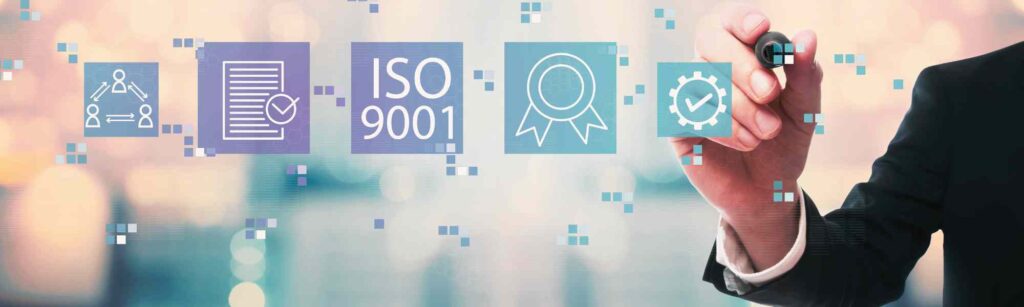
The Challenge of Obtaining ISO 9001:2015 Certification
While ISO 9001:2015 certification offers numerous benefits, obtaining it is no small feat. Manufacturers must navigate a rigorous process that typically includes the following steps:
1. Initial Assessment: The first step involves a thorough assessment of the existing quality management system against ISO 9001:2015 requirements. This gap analysis identifies areas that require improvement or adjustment.
2. Documentation: Manufacturers must develop and implement a comprehensive quality management system, including quality policies, procedures, and work instructions. Documentation must align with ISO 9001:2015 standards.
3. Training and Awareness: Staff at all levels need to be trained and made aware of the quality management system’s requirements and their roles in its implementation.
4. Internal Auditing: Regular internal audits are conducted to ensure compliance with ISO 9001:2015 standards and identify opportunities for improvement.
5. Certification Audit: An accredited third-party certification body conducts a thorough audit of the manufacturer’s quality management system. The manufacturer must demonstrate compliance with ISO 9001:2015 requirements.
6. Continuous Improvement: Even after certification, the manufacturer must continually assess and enhance its quality management system, ensuring ongoing adherence to ISO 9001:2015 standards.
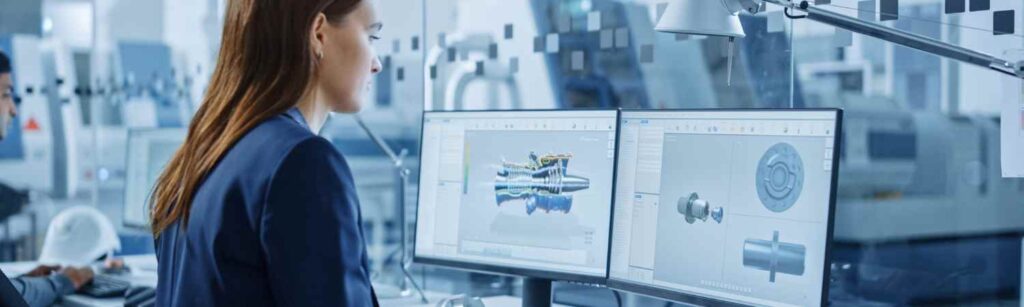
Optmel’s ISO 9001:2015 Certification
Optmel’s achievement of ISO 9001:2015 certification is significant because it underscores our unwavering commitment to quality, customer satisfaction, and operational excellence. Here are some reasons why this certification is a cause for celebration:
1. Enhanced Credibility: ISO 9001:2015 certification provides third-party validation of Optmel’s commitment to quality.
2. Improved Efficiency: The ISO 9001:2015 framework encourages process optimization and efficiency. Optmel’s adherence to these principles can result in reduced waste, improved resource utilization, and cost savings.
3. Customer Confidence: Customers can have greater confidence in Optmel’s products and services, knowing they meet rigorous international quality standards.
4. Market Access: ISO 9001:2015 certification has opened doors to new markets and opportunities, as many of our global clients prefer to work with certified suppliers.
5. Continuous Improvement: Optmel’s commitment to ISO 9001:2015 is a commitment to ongoing improvement. This ensures that our customers’ products and services remain competitive and relevant in an ever-changing marketplace.
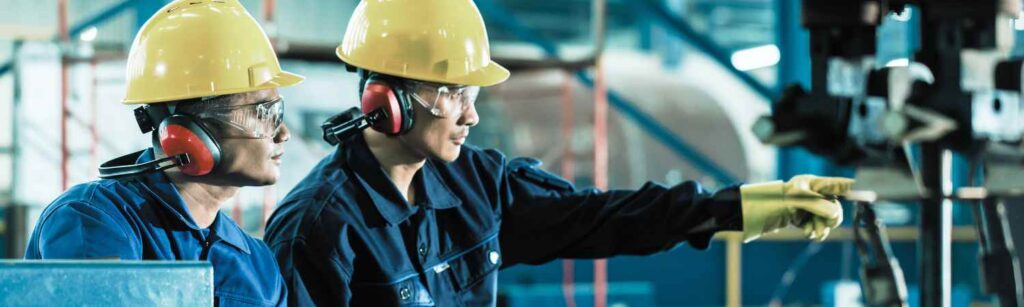
Why Choose Optmel As Your Manufacturing Partner
ISO 9001:2015 certification is a hallmark of quality and excellence in the manufacturing industry. Optmel’s ISO 9001:2015 certification is a testament to our commitment to quality, and it positions us well in the competitive world of manufacturing, ultimately benefiting our customers.
Contact us today if you are interested in learning more about our certifications and how our manufacturing and engineering services can serve you.
Leave a Reply